Rotary
CONTINUOS ROTARY FILLER
Rotary filler represents the most modern technology of filling for liquid , dense or semi-dense products with high and low viscosity. They are based on the use of magnetic flowmeters of inductive (volumetric filling) or mass type (filling by weight) with a filling accuracy of the 0,2%. Our range of rotary fillers is able to respond effectively to production needs, ranging from a minimum of 12 to a maximum of 60 filling valves with a maximum productivity of 600 bpm.
MAIN FEATURES:
• Stainelss steel AISI 304 mechanical structure
• Duplex or super duplex version for corrosilve products with total closure and fume extraction system
• Atex version for highly flammable products
• Parts in direct contact with the products in stainless steel AISI 316/L
• Absence of tank on the machine the product is fed to the machine directly from the silos by means of a suitable sized pump managed by a P.I.D control system the closed circuit dosage system prevents the contamination of the product with external agents
• Washing (CIP) and sterilization (SIP) performed automatically from the panel without the need to disassembled the components, a removable tray collects the washing solution
• Dosing valves built in stainless steel AISI316, sanitary and removable with tri-clamps collars to facilitate cleaning and maintenance operations.
• Standard version with conical shutter dosing valves suitable for non-foaming , liquid dense or semi-dense products.
• Version with servo-motorized plates and plunger nozzle valves for foaming liquid products: this technology allows filling from the bottom of the bottle by means of a vertical movement of the plate, avoiding the formation of the foam during the process.
• Controlled system of the dosed bottle and automatic reject, the non-dosed bottle is rejected and sent to a parallel conveyor at the exit of the machine.
• Brushless motorized bottle entry scroll with electronic cam movement with the possibility of preventing the bottle entrance in phase (for example for maintenance or exclusion of a dosing valve)
• Controlled of the dosed quantity directly from the operator panel
• Standard version with inductive magnetic flow meter suitable for all products with a minimum electrical conductivity of 5 µS/cm
• Version with mass type flow meters suitable for products with a low electrical conductivity (oils, creams etc)
• Duplex or super duplex version for corrosilve products with total closure and fume extraction system
• Atex version for highly flammable products
• Parts in direct contact with the products in stainless steel AISI 316/L
• Absence of tank on the machine the product is fed to the machine directly from the silos by means of a suitable sized pump managed by a P.I.D control system the closed circuit dosage system prevents the contamination of the product with external agents
• Washing (CIP) and sterilization (SIP) performed automatically from the panel without the need to disassembled the components, a removable tray collects the washing solution
• Dosing valves built in stainless steel AISI316, sanitary and removable with tri-clamps collars to facilitate cleaning and maintenance operations.
• Standard version with conical shutter dosing valves suitable for non-foaming , liquid dense or semi-dense products.
• Version with servo-motorized plates and plunger nozzle valves for foaming liquid products: this technology allows filling from the bottom of the bottle by means of a vertical movement of the plate, avoiding the formation of the foam during the process.
• Controlled system of the dosed bottle and automatic reject, the non-dosed bottle is rejected and sent to a parallel conveyor at the exit of the machine.
• Brushless motorized bottle entry scroll with electronic cam movement with the possibility of preventing the bottle entrance in phase (for example for maintenance or exclusion of a dosing valve)
• Controlled of the dosed quantity directly from the operator panel
• Standard version with inductive magnetic flow meter suitable for all products with a minimum electrical conductivity of 5 µS/cm
• Version with mass type flow meters suitable for products with a low electrical conductivity (oils, creams etc)
Our filler can be integrated in monobloc combined with one or more capping turrets
- Several capping turrets can be integrated inside the same monobloc in order to be able to apply different closures on the same bottle
- Electronic rotary capping turrets with servo-motorized tightening units
- Rotary turrets from 4 to 24 capping heads for a maximum productivity of 600 bpm
- Interchangeable spindles according to the type of cap with replaceable knurled or rubberized terminals
- Electronic tightening units with brushless motorization controlled by an electronic cam
- Cam set by recipe based on cap type, bottle height and tightening setting
- Mechanical screwing with hysteresis clutches or servo motorized with torque control
- Caps feeding with rotary mechanical sorter
- Dispenser caps, screw caps, flip top and trigger processing
- Several capping turrets can be integrated inside the same monobloc in order to be able to apply different closures on the same bottle
- Electronic rotary capping turrets with servo-motorized tightening units
- Rotary turrets from 4 to 24 capping heads for a maximum productivity of 600 bpm
- Interchangeable spindles according to the type of cap with replaceable knurled or rubberized terminals
- Electronic tightening units with brushless motorization controlled by an electronic cam
- Cam set by recipe based on cap type, bottle height and tightening setting
- Mechanical screwing with hysteresis clutches or servo motorized with torque control
- Caps feeding with rotary mechanical sorter
- Dispenser caps, screw caps, flip top and trigger processing
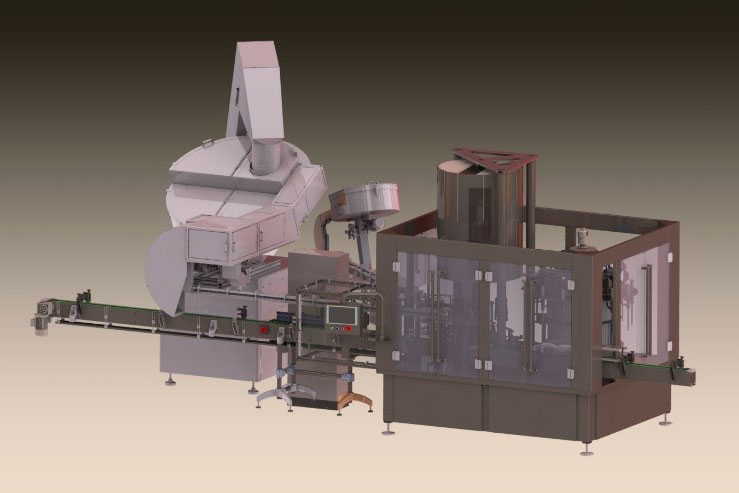
Request a quote for
CONTINUOS ROTARY FILLER
Fill this form